An interview with Professor Dr.-Ing. Andreas Griesinger, director of the Steinbeis Transfer Center for Heat Management in Electronics
Heat management involves applications in many areas, as Professor Dr.-Ing. Andreas Griesinger explains in an interview with TRANSFER. A winner of the Löhn Award, Griesinger provides some interesting insights into the precise methods used to measure thermal interface materials, the current requirements of heat management in electronics, and how digital solutions are changing this field of technology.
Hello Professor Griesinger. In 2013 your Steinbeis Transfer Center won the Steinbeis Foundation Transfer Award – the Löhn Award, with Behr GmbH & Co. KG for the development of an ultraprecise system for measuring thermal interface materials. In what way was your solution innovative?
The special thing about the solution was that for the first time we managed to combine highly precise mechanical engineering with electronics and corresponding instrumentation. The device we developed was the first to simultaneously show the exact thermal and flow properties of samples exposed to thermal and mechanical stress. It means you can use the kind of highly precise mechanical movements needed to characterize certain materials under real application scenarios, while at the same time taking exact measurements such as temperatures, resistance, layer thicknesses, etc.
How did your partnership with Behr come about and what happened to the collaboration after the award?
We’re not really sure how exactly we came to work with one another. All I can say is that we’ve known Behr for a long time, also because they’re based near where we are in Feuerbach in Stuttgart, just a few kilometers from us as the crow flies. They also work on the same topics as us. Behr is a big company and since MAHLE acquired a majority interest in it, it’s been a global enterprise. In any case, at some point there was a meeting with the people at Behr and it was worked out that we’re both trying to solve the same problem, so this led to collaboration and the partnership is still going strong. We basically developed a device together and stay in touch so that we can keep exchanging ideas.
Of course, the transfer award helped us become known in the area. Two years ago, people sent us lots of samples from all around the world to take measurements, which is what our Steinbeis Enterprise offers as a service. And at some point a famous automotive company approached us and now virtually every material they use has to go through our laboratory. That was and still is a huge success and it creates lots of leads for us.
Increasing international awareness of environmental issues, demands for more sustainable solutions and lower energy consumption – these all spell new demands when it comes to heat management in electronics. Where do you think the biggest challenges lie, and how will the measurement process you’ve developed help address these challenges?
There are a number of buzzwords going around at the moment when people talk about new tech: autonomous driving for example, and of course electric vehicles overall – e-mobility. These are huge challenges because they entail so many open technology issues. In terms of how that affects our thermal interface materials, or our device, one of the big issues is service life. People aren’t really sure how these new materials will behave in the long term. The materials themselves aren’t actually that new; what’s new is the requirements they have to meet in cars. What this means is that certain thermal stresses overlap with certain mechanical stresses and we don’t know enough about how these interact. But producers also want to move quickly into serial production. It’s quite possible that a good number of us will be driving electric vehicles in the near future; at least there are plans in the pipeline for high volumes of electric cars. So the big question is, how long will these cars actually last? That’s the challenge, and our device has already made an important contribution in this area, first of all by precisely characterizing the materials. We know exactly how these materials will behave and the material properties this stems from. We can use this information to carry out calculations and interpret properties exactly. The other factor is what this device is now capable of. It has a feature that was only added afterwards. It runs through certain modes, specific kinds of testing procedures, to gather information on durability. So I can use certain types of accelerated procedures, which then allow me to work out how long the material will last in actual applications.
What are the current trends in heat management and electronic systems, and what impact will these have on the services offered by your Steinbeis Enterprise? In what way will your projects or the briefs customers come to you with change?
The trends are very clear – they’re pointing us to words that reflect the zeitgeist at the moment: digital transformation and Industry 4.0 (connected manufacturing). One thing that no-one really knows is what underpins this – ultimately it’s always hardware, and what underpins that is heat management. Here’s an example to demonstrate what I mean. They say that the volume of data going through the internet doubles every 18 months. Data volume is synonymous with servers and those big rooms they keep computers in. And this is precisely where heat management is so important, because heat is sometimes an even bigger problem than the actual design of all the electronics. So in this respect, our services revolve precisely around the most important aspect.
Another interesting issue is energy dissipation. Because more and more information is now being transferred and companies need bigger and bigger computers, more and more energy is being wasted. And another thing that could become a trend is the re-use of energy, especially the energy that inevitably goes to waste when operating larger server facilities, computers, or electric cars. At the moment, heat is simply allowed to dissipate into the surroundings, which ultimately is a waste. But there are already some interesting projects looking into reusing lost energy, for example in cars or in server rooms. As far as our services in this area are concerned, our Steinbeis Enterprise is more into the fundamentals, so we kind of take one step back. We look more at the materials, material values, the cooling concepts. But there has also already been a collaborative project with the DLR to look at using the heat given off by electric cars to provide air conditioning in the interior.
As for the tasks our Steinbeis Enterprise will work on in the future, we work in the field of heat management and we want to stay there because it’s where we feel most comfortable. Our job is to identify concepts and develop them in order to optimize thermal design. That means analyzing and optimizing heat flow paths. A big area – that’s getting bigger and bigger – is service life or durability, and as I said the question is how will these materials last under certain conditions and how should we predict this as accurately as possible. These are the topics we think about every day and they’ll continue to occupy us in the future.

The measurement system that won the Steinbeis Foundation Transfer Award is used to characterize
thermal interface materials
Contact
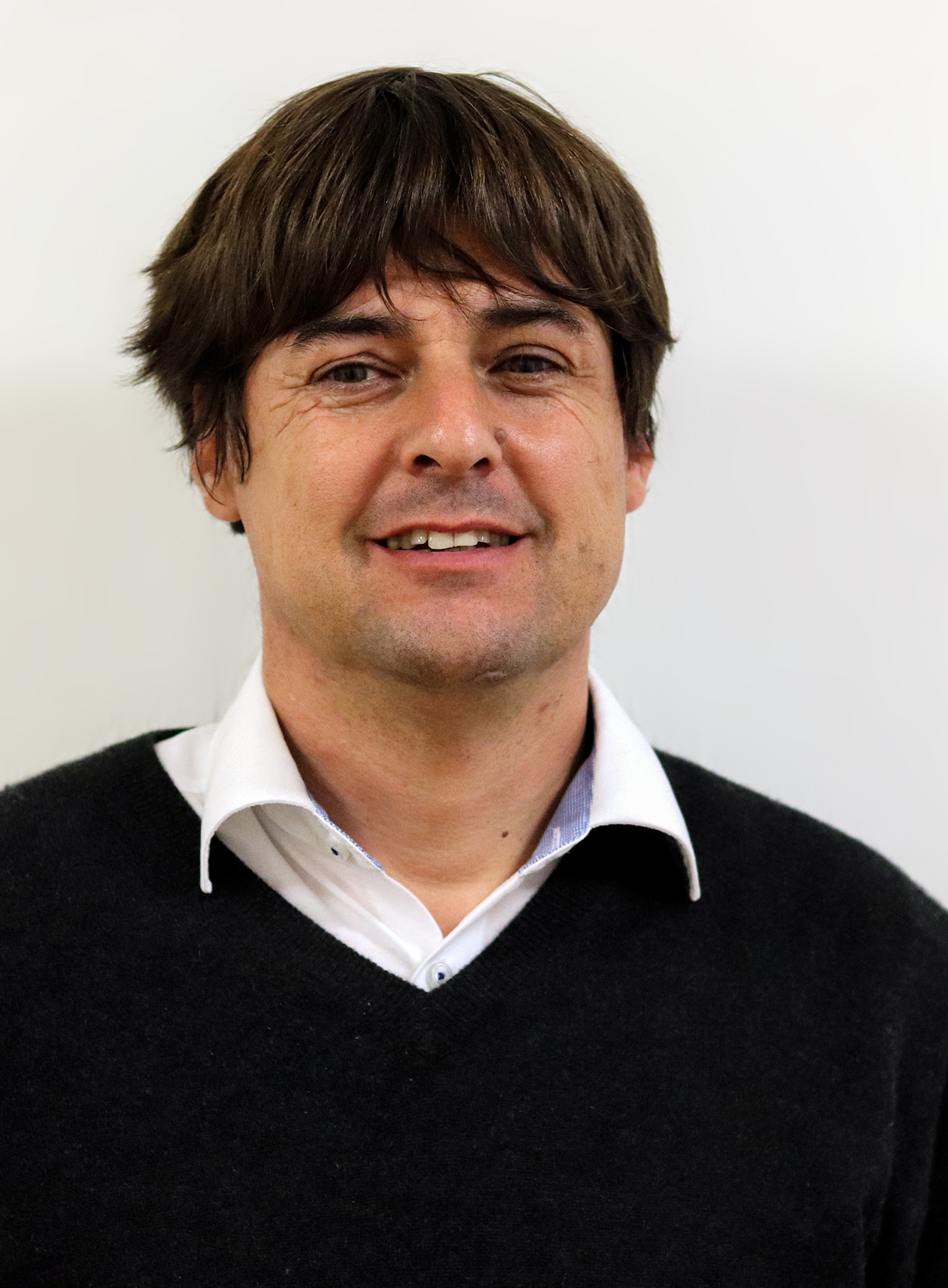
Professor Dr.-Ing. Andreas Griesinger
Professor Dr.-Ing. Andreas Griesinger is director of the Steinbeis Transfer Center for Heat Management in Electronics and the Steinbeis Innovation Center for Heat Management at the Baden- Wuerttemberg Cooperative State University in Stuttgart. His Steinbeis Enterprise offers its clients a comprehensive range of services relating to heat management and durability testing involving electronic components and systems.
Professor Dr.-Ing. Andreas Griesinger
Steinbeis Transfer Center Heat Management in Electronics (Walddorfhäslach)
www.zfw-stuttgart.de