Im Gespräch mit Professor Dr.-Ing. Andreas Griesinger, Leiter des Steinbeis-Transferzentrums Wärmemanagement in der Elektronik
Wärmemanagement hat vielfältige Einsatzmöglichkeiten, das zeigte Professor Dr.-Ing. Andreas Griesinger im Gespräch mit der TRANSFER. Als Preisträger des Löhn-Preises gab er Einblick, wie man thermische Interfacematerialien präzise messen kann, welche Anforderungen aktuell an das Wärmemanagement in der Elektronik gestellt werden und wie die Digitalisierung diesen Bereich beeinflusst.
Herr Professor Griesinger, 2013 gewann Ihr Steinbeis-Transferzentrum gemeinsam mit der Behr GmbH & Co. KG den Transferpreis der Steinbeis-Stiftung – Löhn-Preis für die Entwicklung eines hochpräzisen Systems zur Messung von thermischen Interfacematerialien. Welche Innovationen stecken dahinter?
Das Besondere war die erstmalige Kombination des hoch präzisen Maschinenbaus mit der Elektronik und der entsprechenden Messtechnik. Mit dem entwickelten Gerät konnten zum ersten Mal gleichzeitig die thermischen Eigenschaften und das Fließverhalten der Proben unter thermischer und mechanischer Last genau analysiert werden. Das bedeutet, man kann hochpräzise mechanische Bewegungen durchführen, die für die Charakterisierung von bestimmten Materialien unter realen Einsatzbedingungen notwendig sind, und gleichzeitig auch entsprechende Größen, wie Temperaturen, Widerstände, Schichtdicken etc., präzise erfassen.
Wie kam es zu Ihrer Partnerschaft mit der Behr GmbH und wie hat sich diese Zusammenarbeit weiterentwickelt?
Wie es genau dazu gekommen ist, lässt sich gar nicht mehr so richtig nachvollziehen. Jedenfalls war die Behr GmbH uns schon lange durch die räumliche Nähe bekannt, das Unternehmen hat seinen Sitz in Stuttgart- Feuerbach, ein paar Kilometer Luftlinie von uns entfernt, und arbeitet am gleichen Themengebiet. Behr ist ein großer Konzern – Weltkonzern mittlerweile, da die MAHLE GmbH inzwischen die Mehrheit an Behr übernommen hat. Jedenfalls kam es irgendwann zu einem Treffen mit den Behr-Mitarbeitern, und dabei wurde festgestellt, dass wir an der Lösung des gleichen Problems arbeiten, und so kam es zu dieser Zusammenarbeit, die auch immer noch anhält: Wir haben das Gerät gemeinsam weiterentwickelt und sind in Kontakt, so dass der Austausch immer da ist.
Natürlich hat uns der Transferpreis geholfen, in dem Bereich bekannt zu werden. Vor zwei Jahren haben wir viele Proben aus der ganzen Welt zur Messung zugeschickt bekommen, die unser Steinbeis-Unternehmen als Dienstleistung anbietet. Irgendwann hat sich dann ein namhafter Automobilhersteller an uns gewandt und mittlerweile muss quasi jedes Material, das dort eingesetzt wird, bei uns durchs Labor. Das war und ist natürlich ein großer Erfolg und bringt uns viele neue Anfragen.
Das weltweit zunehmende Umweltbewusstsein, die Forderung nach Nachhaltigkeit und danach, weniger Energie zu verbrauchen, stellen neue Anforderungen an das Wärmemanagement in der Elektronik. Wo sehen Sie die größten Herausforderungen und wie kann das von Ihnen entwickelte Messsystem helfen diese erfolgreich zu meistern?
Es gibt aktuell ein paar Stichworte, die man immer hört, wenn es um neue Technologien geht: autonomes Fahren zum Beispiel und natürlich die gesamte E-Mobility. Das sind die großen Herausforderungen, da es dazu viele offene technische Fragen gibt. Bezogen auf unsere thermischen Interfacematerialien beziehungsweise auf unser Gerät, ist eine der großen Fragen dabei die Lebensdauer. Man weiß noch nicht so richtig, wie sich diese neuen Materialien im Auto auf Dauer verhalten. Die Materialien an sich sind gar nicht neu, aber das Neue sind die Anforderungen im Auto. Das bedeutet, dass bestimmte thermische Belastungen mit bestimmten mechanischen Belastungen überlagert werden und dieses Zusammenspiel ist noch unbekannt.
Allerdings möchten die Hersteller auch schnell in Serie gehen: Es kann sein, dass einige von uns in den nächsten Jahren elektrisch fahren, auf jeden Fall sind große Volumen bei den Elektroautos geplant, die vom Stapel gehen. Die ganz große Frage dabei lautet: Wie lang halten diese Autos? Das ist die Herausforderung und unser Gerät hat dazu schon einen großen Beitrag geleistet, erst einmal um die Materialien genau zu charakterisieren: Man weiß genau, wie sich diese Materialien verhalten, welche Stoffwerte dahinter stecken. Mit diesen Daten können wir dann entsprechend rechnen und sie präzise auslegen. Das Zweite, was dieses Gerät mittlerweile kann, ist ein Feature, das erst zusätzlich nachträglich eingebaut wurde: Hier werden bestimmte Modi, bestimmte Prüfabläufe durchgeführt, um Informationen über die Lebensdauer zu erhalten. Ich kann also bestimmte beschleunigte Verfahren anwenden, mit denen ich dann Rückschlüsse ziehen kann, wie lang das Material im realen Einsatz hält.
Was sind die aktuellen Trends im Wärmemanagement elektronischer Systeme und wie werden diese das Dienstleistungsangebot Ihres Steinbeis-Unternehmens beeinflussen? Wie verändern sich dann Ihre Projekte oder die Aufgabenstellungen, mit denen Kunden kommen?
Die Trends sind ganz klar, wir sind da bei den Stichworten, die den Zeitgeist gerade ausmachen: Digitalisierung und Industrie 4.0. Was niemand richtig weiß: Was dahinter steckt, ist letztlich immer Hardware und dahinter steckt das Wärmemanagement. Ein Beispiel, um das zu verdeutlichen: Man sagt, dass sich das Datenvolumen, das durch das Internet geht, alle 18 Monate verdoppelt. Und Datenvolumen ist gleichzusetzen mit Servern, mit großen Räumen, in denen die Rechner aufgestellt sind. Und genau an dieser Stelle ist das Wärmemanagement von großer Bedeutung, denn dieses ist zum Teil sogar ein größeres Problem als das elektronische Design. Insofern setzen wir mit unseren Dienstleistungen genau an diesen Schlüsselstellen an.
Ein weiteres spannendes Thema ist die Verlustleistung: Da immer mehr Daten transferiert und immer größere Rechner gebraucht werden, entsteht immer mehr Verlustleistung. Und was auch zum Trend werden kann ist, dass man die Energie wieder nutzt, die zwangsläufig abfällt, wenn man größere Serverräume betreibt oder auch Rechner oder Elektroautos. Aktuell wird die Wärme einfach in die Umgebung abgegeben, sie ist letztlich Abfall. Es gibt aber schon einige interessante Projekte, um diese Verlustleistung, zum Beispiel beim Auto oder beim Serverraum, wieder weiterzuverwenden. Was unsere Dienstleistungen zu diesem Thema angeht, so sind wir mit unserem Steinbeis-Unternehmen eher an den Grundlagen dran, quasi eine Stufe davor: Wir betrachten mehr die Materialien, die Stoffwerte, die Kühlkonzepte. Aber es gab auch schon eine Kooperation mit der DLR, wo es darum ging, die Abwärme vom Elektroauto zu nutzen und für die Kabinenklimatisierung zu verwenden.
Was die zukünftigen Aufgabenstellungen für unser Steinbeis-Unternehmens angeht, so sind wir im Feld Wärmemanagement und wollen auch dort bleiben, dort fühlen wir uns wohl. Unsere Aufgabe besteht darin, Konzepte zu finden, zu entwickeln, um das thermische Design zu optimieren. Das heißt, Wärmepfade zu analysieren und zu optimieren. Ein großes Thema, was immer mehr kommt, ist wie bereits erwähnt das Thema Lebensdauer oder die Frage, wie lange hält der Stoff unter bestimmten Bedingungen und das entsprechend präzise vorauszuberechnen. Das sind die Themen, die uns aktuell beschäftigen und auch in der Zukunft beschäftigen werden.

Das mit dem Transferpreis der Steinbeis-Stiftung ausgezeichnete Messsystem zur Charakterisierung
thermischer Interfacematerialien
Kontakt
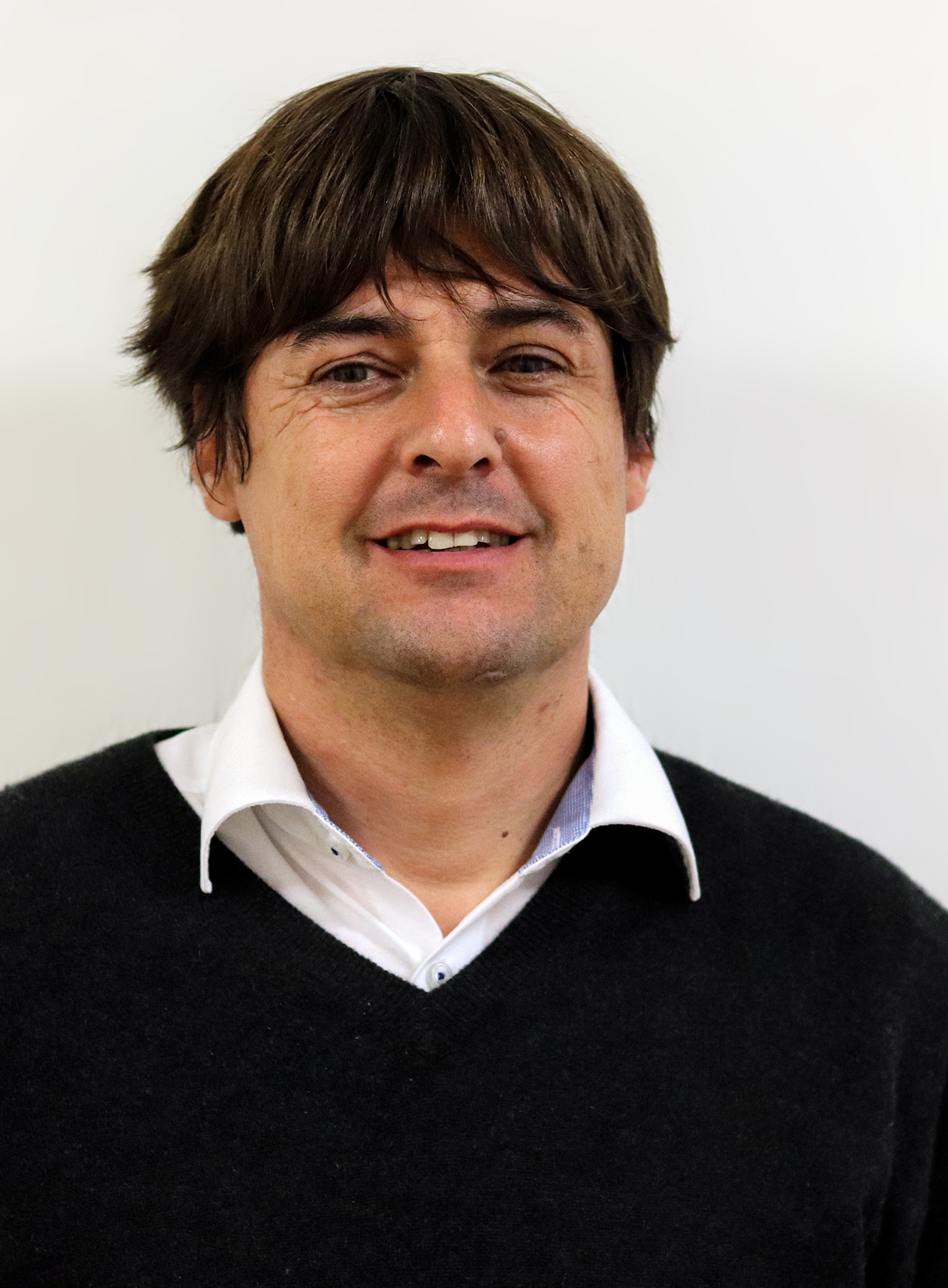
Professor Dr.-Ing. Andreas Griesinger
Professor Dr.-Ing. Andreas Griesinger ist Leiter des Steinbeis- Transferzentrums Wärmemanagement in der Elektronik und des Steinbeis-Innovationszentrums Wärmemanagement an der Dualen Hochschule Baden-Württemberg Stuttgart. Die Steinbeis- Unternehmen bieten ihren Kunden umfassende Leistungen im Bereich Wärmemanagement und Lebensdaueruntersuchung elektronischer Komponenten und Systeme.
Professor Dr.-Ing. Andreas Griesinger
Steinbeis-Transferzentrum Wärmemanagement in der Elektronik (Walddorfhäslach)
www.zfw-stuttgart.de