An interview with Professor Dr.-Ing. Harald Augustin, director of the Steinbeis Transfer Center for Process Management in Product Development, Production and Logistics
Professor Dr.-Ing. Harald Augustin talked to TRANSFER magazine about future changes in production and logistics as a result of digital transformation and the importance of “free thinking.”
Hello Professor Augustin, digital technology is changing manufacturing processes and thus also the world of work. Where do you see the biggest challenges for companies with this new situation?
There are three key challenges that come with digital transformation and at the same time, they’re success factors for businesses: finding the right business strategy for digital transformation and communicating this transparently; seeing processes in new ways and thinking freely or disruptively; fostering know-how among staff and developing this knowledge.
Managers need a digital transformation strategy that covers all areas of the business. Without this, there can be no synergy effects between different departments or at the overlapping areas between processes. Also, everyone at a company has to be clear about where the journey is taking them. This is the only way to allay hidden fears and motivate people to do something themselves. So transparency is the be-all and end-all. Digital solutions need to be seen as a driver or enabler of new innovation and improvement. This means firms have to find out which digitalization technologies offer new opportunities for the business, not just in the here and now but also in the future. The key thing is to identify how digitalization can improve existing processes but also which emerging business models and opportunities it can create. “Free thinking” or thinking in terms of disruption are an important element of this. My personal preference is to use the term “free thinking,” because that’s what you need to achieve disruption – i.e., radical renewal – in the first place. But how many companies actually provide enough leeway for this to happen at the moment? Big companies go on the journey by “buying in” free thinking: They acquire startups. Things are different at small and medium-sized enterprises, who have to go on the journey themselves. This brings us directly to the third and perhaps decisive success factor, which often feels like a restraint or an obstacle to future development: fostering know-how among employees and developing this knowledge. Even in an era of digital technology, people will still be the cornerstone of success. This is because human beings are highly flexible in action and thought. Future possibilities for applying artificial intelligence (AI) are still quite limited, even for the next couple of decades. The changes we need can only be driven and implemented by people. Digital solutions will only be a means to an end, whether it’s about optimization or establishing new business models using IT or AI. The question you always meet is whether staff have the right qualifications to exploit the opportunities presented by digital technology and make use of it. So staff need training on a variety of fronts. They need technical expertise – an understanding of how to use the technologies of digital transformation – and they need method skills, which is about knowing how to use digital technology to optimize and redesign processes, structures, and business models – and this expertise needs expanding. I know from my own experience in projects that not enough is being done to invest in these two areas of competence. This is a fatal mistake and it will come back to haunt companies in the medium term, because digital transformation accelerates development at breakneck speed, so skills development has to be continuous. Otherwise, you’re actually moving backwards.
Among other things, your Steinbeis Enterprise offers customers the possibility to set up virtual work environments. What sort of problems do your customers ask you about? Are they sufficiently prepared for changes in the world of work?
The problems they face are still the classic ones: factory planning (new plants or changes), production optimization, lean management, implementation issues, warehouse planning, and logistical systems optimization. I don’t think there’ll be much change in this regard, not on a fundamental level, because ultimately digital solutions are a means to an end. For the projects I’m involved in we use the classic methods and tools for planning and optimizing systems, but we also use the instruments offered by digital factories. So we plan processes and layouts in virtual environments, for example using 3D planning systems and visualization processes. If we’re designing a factory or warehouse or we’re optimizing processes, and it makes sense to use systems revolving around digital manufacturing (such as robot systems), we’ll certainly make use of those technologies. Then there are automated and intelligent material flow systems (things like autonomous and swarm-based ground transport equipment or driverless tugger trains) as well as state-of-the-art IT methods such as data mining and warehouse management systems. Whenever we can, we tap into the possibilities offered by digital technology – not just to make planning more efficient and effective, but also so that processes can be automated and made digital. One highlight this year was a project which involved developing a digital transformation strategy for a company as a basis for planning factory optimization projects, like a kind of roadmap. It turned out that the success factors and challenges that were identified for the project were the right ones and that things wouldn’t be easy during implementation.
Unfortunately, most companies have had such good order pipelines for such a long time now that capacities have been tight, so they’ve not had the time and energy to put thought into digital transformation. They’ve got some ideas and concepts in mind, but if you ask them to be more specific, you never get a clear answer on where the journey will be taking them. This is where things go full circle when it comes to the challenges and key success factors I mentioned – the companies are not working on them, or not directly. There’s no proper foundation for tackling this topic strategically or making things happen. So when we’re working on a project, we try to provide them with lots of ideas and suggestions, so at least we can plug the knowledge gaps with our own know-how. In lots of cases, we use in-house seminars to dovetail these with skills training for the staff involved in projects. We do this to empower businesses to do their own digital technology planning and implementation in the future – without the support of others.
Logistical processes are also undergoing important changes at the moment as a result of digital transformation. What are the trends at the moment in your area of industry, and what direction do you think future developments will take us in?
The current trends are toward end-to-end IT-based process chains in the supply chain, big data, data mining, smart automation with driverless vehicles in production or the warehouse, human-machine collaboration (for example exoskeletons to provide support with lifting loads), digital planning, and warehouse modeling, etc. There are two key areas of development: On the one hand, there’s smart automation involving all kinds of processes carried out routinely by human beings, or processes that are not complicated. Then there’s the aspect of managing the unbelievably high volumes of data companies have access to. The first area is more or less about keeping up the rapid momentum of developments until now regarding automation. In the second area regarding data, this isn’t necessarily something new, but it was only a couple of years ago that it started to receive more attention – and most companies are still quite weak in this area. Data analysis and the subsequent process of data synthesis – i.e., forging a link between the information and the derivation of actual measures – are an unbelievably important skill that has to be mastered, especially in logistics. There’s a huge amount of catching up to do, not just at the universities but also within companies.
Just one last question: Your work revolves around holistic methods and participation – how is this changing in times of digital technology?
In essence, there’s nothing different about our approach when it comes to closely involving people in the workshops when we’re planning and optimizing things, or trying to pinpoint the best solution together in a way that everyone can live with. Everything revolves around people, including in digital transformation. They’re the ones who sponsor innovation and implement it. We’ve always used technology as an enabler – it’s the area I did my PhD in, and the whole concept has been close to my heart ever since. But of course compared to only 20 years ago, we now have a lot more tools at our disposal for planning purposes, plus the systems for implementing things. So I’m actually really happy about this – the view we’ve always had, which was always part and parcel of how we’ve approached things, can now be leveraged to the full. Planning is complex and as new aspects of digital technology have come along, it’s gotten even more complex, but the new technologies can be used to shorten planning times. Other changes I envisage will be because the new systems make it possible to collaborate in different physical locations by using virtual spaces, and this simplifies international planning and saves a tremendous amount of time. Ultimately however, there will always be a need for personal interaction, because everything revolves around human beings and the intelligence they derive from “free thinking” – even if this is still a bit of a challenge. As George Bernard Shaw told us, the disadvantage of intelligence is that one is constantly forced to learn something new.
Contact
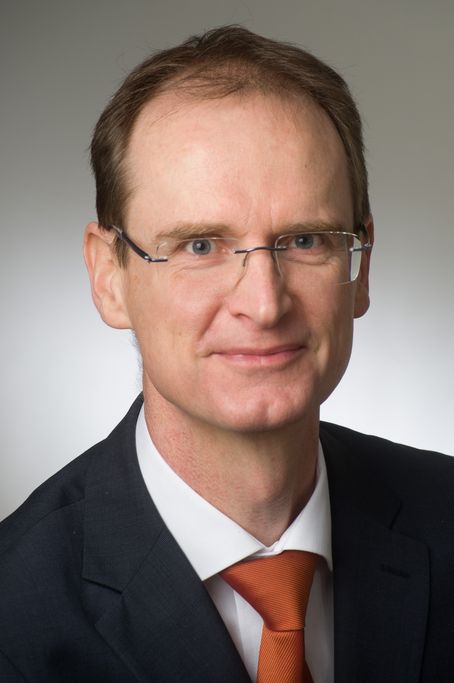
Professor Dr.-Ing. Harald Augustin
Professor Dr.-Ing. Harald Augustin is director of the Steinbeis Transfer Center for Process Management in Product Development, Production and Logistics.. The Steinbeis Enterprise, founded in 2002, specializes in the holistic optimization of processes and technologies, as well as IT systems in production and logistics with the aim of adding value for the customer.
Professor Dr.-Ing. Harald Augustin
Steinbeis Transfer Center Process Management in Product Development, Production and Logistics (Gomaringen)